Kollisionsfreie Bahnplanung für kooperierende Roboter
Die Idee dahinter
Bereits jetzt gibt es automatisierte Fertigungsschritte, in denen zwei oder mehr Roboter zusammenarbeiten, um gemeinsam eine Aufgabe zu erledigen.
Der Aufbau des Systems
Das am ZLP in Augsburg entwickelte System kann in einem virtuellen Abbild der Fertigungsumgebung kollisionsfreie Transportpfade finden.
Anwendungen
Das System wird hauptsächlich bei pick-and-place-Anwendungen eingesetzt, bei denen zwei Roboter einen Kohlenstofffaserzuschnitt von einem ebenen Aufnahmetisch in eine dreidimensional gekrümmte Form transportieren müssen. Es ist aber auch in der Lage, kollisionsfreie Bahnen für einen Roboter zu finden und kann daneben für die Handhabung von anderen Materialien wie zum Beispiel Aluminiumblechen verwendet werden.
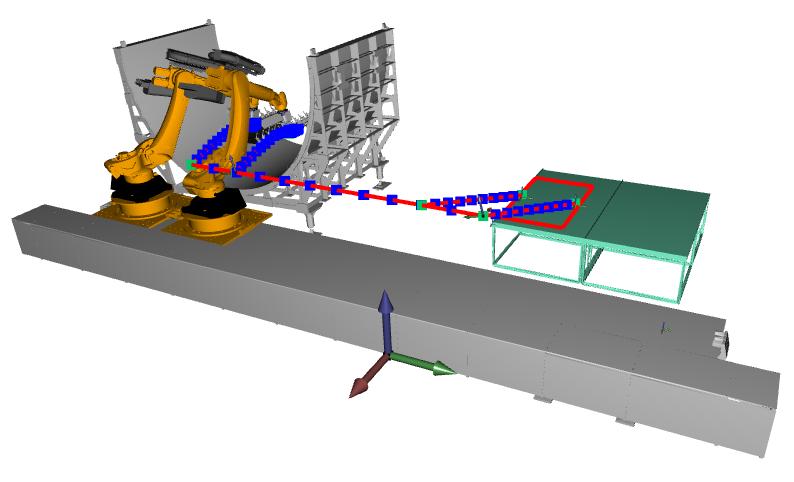
Screenshot des Bahnplanungstools für kooperierende Roboter beim Transport eines Zuschnitts von einem ebenen Tisch in eine zylindrische Halbschale
Ansprechpartner:
Lars Larsen
FlappyBot – der neue Freiheitsgrad für Fiberplacement
Die Idee dahinter
Große, flächige Faserverbundstrukturen für Verkehrsflugzeuge werden aufgrund von Automatisierbarkeit und Prozessstabilität vorwiegend im Fiberplacement-Verfahren hergestellt. Ein typischer Anwendungsfall sind die Flügelschalen.
Der Aufbau des Systems
Der Ansatz frei verfahrbarer, mobiler Einheiten wird seit einer Prämierung durch den DLR-Idea-Award verfolgt. Die zentrale Herausforderung des Verfahrens – dem Fahren auf dem Laminat ohne unzulässige Beschädigungen – wurde auf einem Prüfstand untersucht.
Anwendungen
Für Fiberplacement sind Portalsysteme und Knickarmroboter durch Legeleistung und Genauigkeit Benchmark. Solche Systeme sind durch ihren großen Umfang an Hardware und baulichen Voraussetzungen jedoch nur bedingt skalierbar. Das Projekt FlappyBot hat das Ziel, den Entwicklungsfortschritt der mobilen Robotik für Fiberplacement zugänglich zu machen.
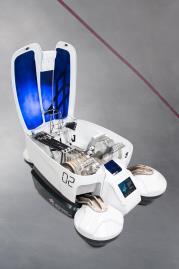
Fiberplacement durch autonome selbstfahrende Einheiten
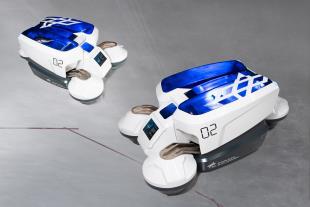
Mehrere Einheiten kooperieren und verfahren ohne Führungskinematik
Ansprechpartner:
Philipp Sämann M.Sc.
Offlineprogrammiersystem für biegeschlaffe Halbzeuge
Die Idee dahinter
Bei der Produktion von Kohlefaserverbundstoffen ist ein wichtiger Schritt die Aufnahme eines zweidimensionalen Zuschnitts aus Kohlefasern und dessen Ablage in einer dreidimensionalen Form.
Der Aufbau des Systems
Das System liest aus einem speziell aufbereiteten Exportfile aus einem CAD-Programm sowohl die 2D- als auch die 3D-Kontur der zu legenden Zuschnitte aus.
Anwendungen
Ursprünglich geplant für das Handling von einfachen kleinen Zuschnitten mit einem Greifer wurde das System weiter entwickelt und kann nun auch mit größeren Zuschnitten umgehen, die von mehreren, auch unterschiedlichen Greifern gegriffen werden müssen. Daneben zeigte es seine Flexibilität, als es auch für die Prozessplanung für das Legen von großen Aluminiumblechen Verwendung fand.
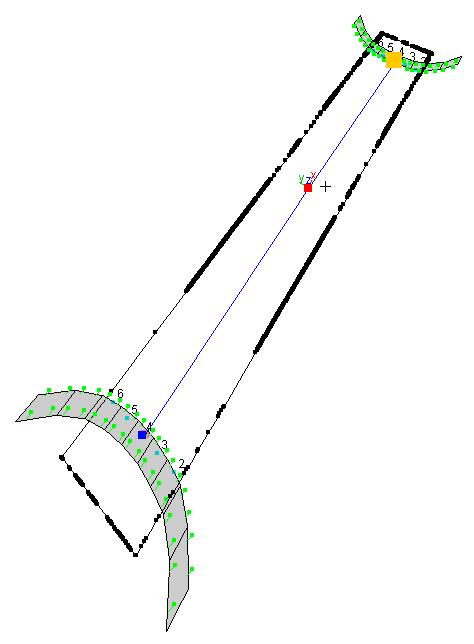
Screenshot des Offlineprogrammiersystems bei der Aufnahem eines Zuschnitts mit zwei gekrümmten Greifern
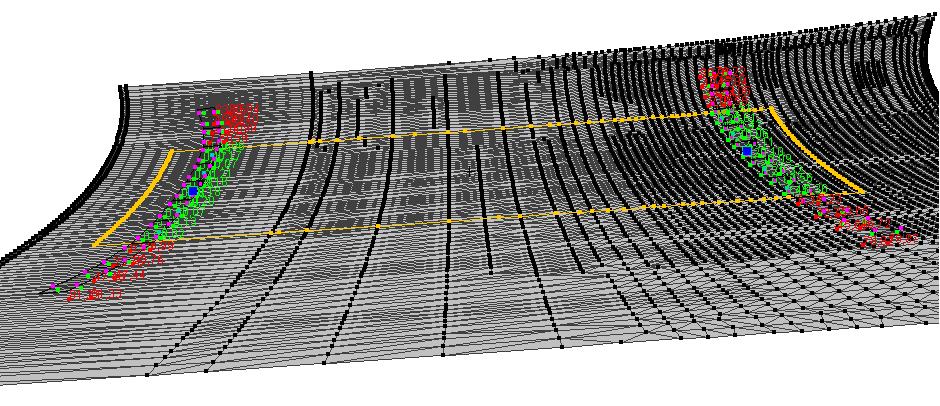
… und der Ablageposition
Ansprechpartner:
Roland Glück
Flexible Montage individueller Baugruppen
Die Idee dahinter
Die individualisierte Fertigung und kürzere Produktlebenszyklen sind aktuelle Trends, die die industrielle Produktion maßgeblich verändern werden. Autonome und kognitive robotische Systeme rücken in den Vordergrund, um die notwendige Flexibilität und Wandlungsfähigkeit für die Produktion der Zukunft zu unterstützen: Die automatisierte Herstellung von Einzelstücken wird möglich.
Der Aufbau des Systems
Das System des DLR basiert auf verschiedenen Planungseinheiten. Zentral sind die Flexibilität und der Grad an Autonomie der Plattform: Ein Algorithmus findet geeignete Montagesequenzen, die von dem System ausgeführt werden können. Methoden zur Greifplanung, die automatische Analyse von Erreichbarkeiten in der Arbeitszelle und die kollisionsfreie Planung von Bewegungen machen das System besonders flexibel – auch mit Blick auf verschiedene Produktvarianten.
Anwendungen
Aktuell baut das System Aluminiumprofile zu komplexen Strukturen auf. Das Design des zweiarmigen Systems zielt darauf ab, die Anzahl der spezialisierten Systemeinrichtungen zu reduzieren und so die Montage von großen und unterschiedlichen Produktfamilien zu ermöglichen. Das System kann verschiedene Produkte fertigen, die über ein einfach zu bedienendes Tablet Interface konfiguriert werden. Folgende Teilaufgaben muss das System erledigen: Profile und Verbindungswinkel platzieren, Einlegemuttern einfügen und Verbindungen zusammenschrauben. Die zwei Roboterarme arbeiten dabei so zusammen, dass diese Aufgaben ohne spezielle Werkstückhalterungen gelöst werden können.
Ansprechpartner:
Korbinian Nottensteiner
Institut:
Safe Autonomous Robotics Assistant (SARA)
Die Idee dahinter
Robotische Fertigungsassistenten müssen gefühlvoll, flexibel und einfach zu bedienen sein – und mehr. Der DLR Safe Autonomous Robotic Assistant soll die robotische Montageunterstützung auf ein neues Level heben.
Der Aufbau des Systems
Eine komplett neue, patentierte Anordnung von Kraft- und Drehmomentsensoren erlaubt die Unterscheidung von Führ- und Kontaktkräften. Per PCI Express kann der Steuerungs PC jederzeit bis in die Spitze des Roboters zugreifen.
Anwendungen
Im Rahmen der Factory of the Future ist SARA die zentrale Komponente für vollständig autonome Montage. Einfache Logistiksysteme und durchdachte passive Elemente reichen, um vollständig autonom für Montageaufträge zu rüsten, und diese abzuarbeiten. Durch die besonderen Fähigkeiten des Arms, zusammen mit der intelligenten Planungssoftware des Instituts für Robotik, werden komplexe Montageaufgaben oder kleine Losgrößen automatisierbar.
Ansprechpartner:
Oliver Eiberger