Robotic Screw Extrusion Additive Manufacturing mit der hybriden Fertigungsanlage Space A
Die Idee dahinter
Die Fertigung von individualisierten Produkten on Demand und die wirtschaftliche Realisierung großer Variantenvielfalt bei kleinen bis mittleren Stückzahlen, bis hin zur Losgröße 1 ist eine stetig an Bedeutung gewinnende Anforderung an die industrielle Produktion.
Der Aufbau des Systems
Die Fertigungsanlage besteht aus zwei gleichwertig flexiblen, sich gegenüberstehenden Modulen, welche je mittels Industrieroboter das entsprechende Werkzeug handhaben. In der Mitte befindet sich ein Dreh-Kipp-Tisch mit beheizbarer Bauplattform. Die Module haben jeweils die Fähigkeiten, mit zwei verschiedenen Extrudern und damit zwei Materialien additiv zu fertigen, mit einer Frässpindel subtraktiv zu arbeiten sowie mit einem Greifer Einlegteile zu platzieren.
Anwendungen
Aufgrund der hohen erreichbaren Aufbauraten eignet sich das Verfahren insbesondere für die wirtschaftliche Kleinserienfertigung. Durch die Nutzung von Standardgranulaten als Ausgangsmaterial und die damit große zur Verfügung stehende Materialpalette sind vielfältige Anwendungsbereiche möglich. Die Spanne reicht hier z.B. von Kopfbügeln für Faceshields aus hautverträglichem Polycarbonat bis zu großvolumigen Fahrzeugkomponenten aus faserverstärktem Polyamid. Zusätzlich erlaubt die Flexibilität der Fertigungszelle die Kombination von additiven mit konventionell hergestellten Strukturen und Einlegeteilen sowie die gezielte abtragende Bearbeitung von Funktionsflächen in einem integrierten Prozess.
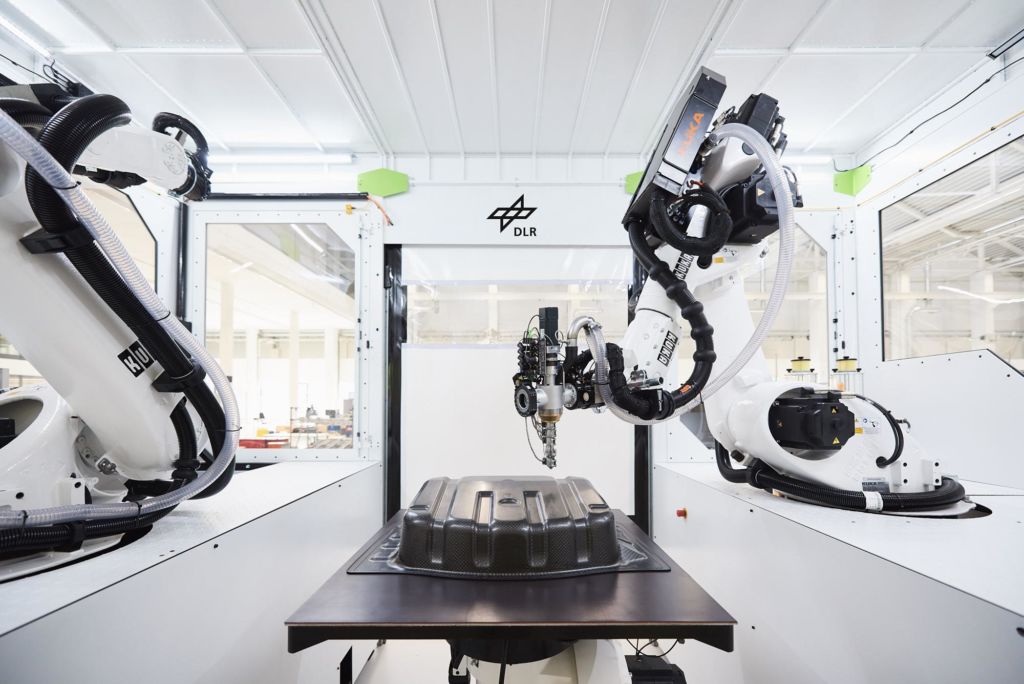
Innenansicht Hybride Fertigungszelle Space A
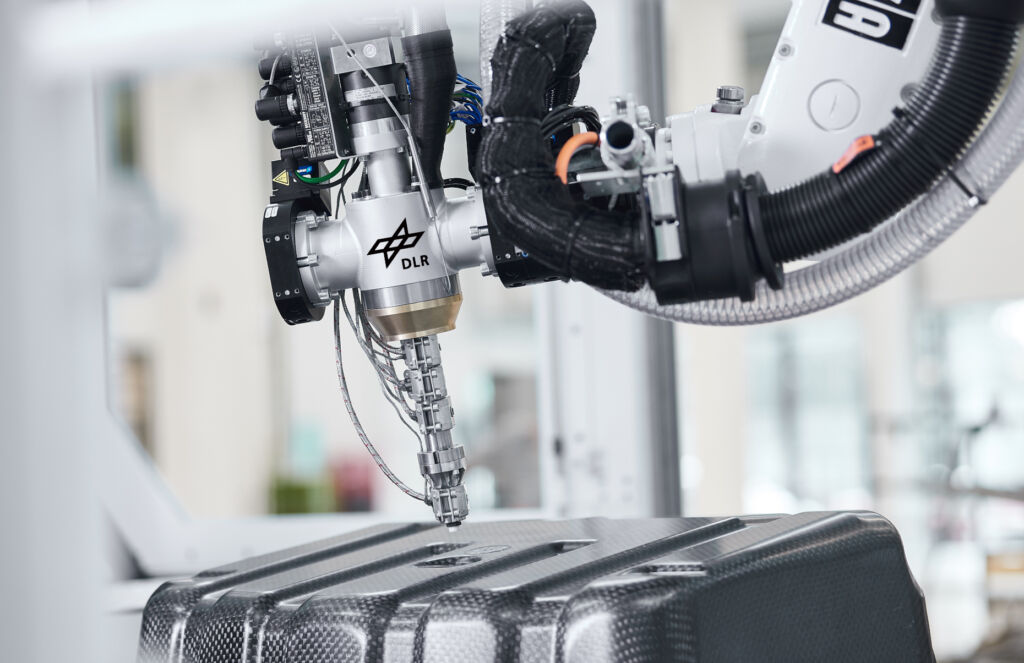
Ansprechpartner:
Nicolas Unger
Institut:
FlappyBot – der neue Freiheitsgrad für Fiberplacement
Die Idee dahinter
Große, flächige Faserverbundstrukturen für Verkehrsflugzeuge werden aufgrund von Automatisierbarkeit und Prozessstabilität vorwiegend im Fiberplacement-Verfahren hergestellt. Ein typischer Anwendungsfall sind die Flügelschalen.
Der Aufbau des Systems
Der Ansatz frei verfahrbarer, mobiler Einheiten wird seit einer Prämierung durch den DLR-Idea-Award verfolgt. Die zentrale Herausforderung des Verfahrens – dem Fahren auf dem Laminat ohne unzulässige Beschädigungen – wurde auf einem Prüfstand untersucht.
Anwendungen
Für Fiberplacement sind Portalsysteme und Knickarmroboter durch Legeleistung und Genauigkeit Benchmark. Solche Systeme sind durch ihren großen Umfang an Hardware und baulichen Voraussetzungen jedoch nur bedingt skalierbar. Das Projekt FlappyBot hat das Ziel, den Entwicklungsfortschritt der mobilen Robotik für Fiberplacement zugänglich zu machen.
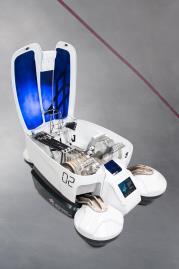
Fiberplacement durch autonome selbstfahrende Einheiten
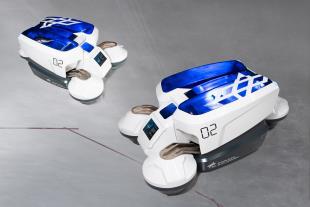
Mehrere Einheiten kooperieren und verfahren ohne Führungskinematik
Ansprechpartner:
Philipp Sämann M.Sc.
Selektives Laserschmelzen
Motivation
Die metallische additive Fertigung („3D-Druck“), z.B. mit Pulverbett-Laserschmelzprozessen (Laser Powder Bed Fusions, LBPF), stellt ein sich rapide weiterentwickelndes Feld dar, welches bereits jetzt erheblichen Einfluss auf die Fertigungswelt von heute ausübt.
Neben der hohen Komplexität, in der LBPF-Prozesse, Werkstoffe, Baustrategien und entstehende Bauteile mit ihren letztendlichen Eigenschaften zusammenhängen, stellt die Prozessüberwachung und Qualitätssicherung aus heutiger Sicht eine wichtige Herausforderung dar. Diese ist notwendig, damit die Verfahren zukünftig robuster und zuverlässiger gestaltet und somit für kritischere Anwendungsbereiche eingesetzt werden können. Prozessüberwachungsverfahren wie z.B. das in situ Melt pool Monitoring können auch einen wichtigen Beitrag zur systematischen Prozess- und Scanstrategieentwicklung für neue Werkstoffe und spezifische Bauteile liefern und das Verständnis der zugrundliegenden Prozess-Bauteil-Material-Zusammenhänge steigern.
Beschreibung
Spezielle Aspekte der Bauteilcharakterisierung und Qualitätssicherung bei der additiven Fertigung metallischer Materialen für Luft- und Raumfahrtkomponenten durch selektives Laserschmelzen (ein LBPF Verfahren) werden in FoF untersucht.
Anwendungsfall
Es wird z.B. die Geometrieabhängigkeit des beim LBPF entstehenden Werkstoffes in einem Turbopumpenimpeller aus Ti-6Al-4V untersucht. Je nach Bauteilgeometrie, z.B. in dünnen im Gegensatz zu massiven Bereichen oder oberhalb von Stützstrukturen, verläuft der Wärmeabfluss der Laserenergie des 3D-Druckprozesses erheblich unterschiedlich.
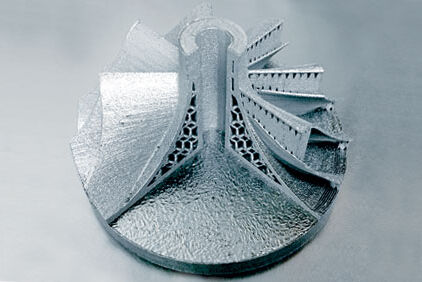
SLM gefertigtes Verdichterrad mit generischen inneren Gitterstrukturen. Im rechten Schaufelblattbereich sind sogn. Stützstrukturen vorhanden, die später entfernt werden müssen.
Ansprechpartner:
Jan Haubrich