Untersuchung zur zukünftigen Kopplung von Roboterzellen an eine digitale Plattform für die Industrie 4.0
Die Idee dahinter
Langfristig sollen über eine digitale Plattform für die Produktentwicklung schon im Entwurf Informationen zur späteren Fertigung, sowohl in technischer als auch betriebswirtschaftlicher Hinsicht, verfügbar werden.
Der Aufbau des Systems
Bisher wurde an der Erstellung einer Ontologie zur Beschreibung eines Robotermontageszenarios gearbeitet. Diese enthält erste Konzepte zur Beschreibung des Montagevorgangs, welche allerdings weiter ausgebaut werden sollen. Zudem existieren eine Datenbank und Schnittstellen, die auf der Ontologie basieren. Einer der nächsten Schritte ist die (prototypische) Anbindung eines oder mehrerer CAD-Tools an einen Montageplaner.
Anwendungen
Aktuell sind in der Ontologie Montageaufgaben für die Montage von individuellen Produkten auf Basis eines Baukastensystems für Aluminiumprofile beschrieben (allerdings noch im Aufbau).
der Planungsaufgabe kann dadurch reduziert werden.
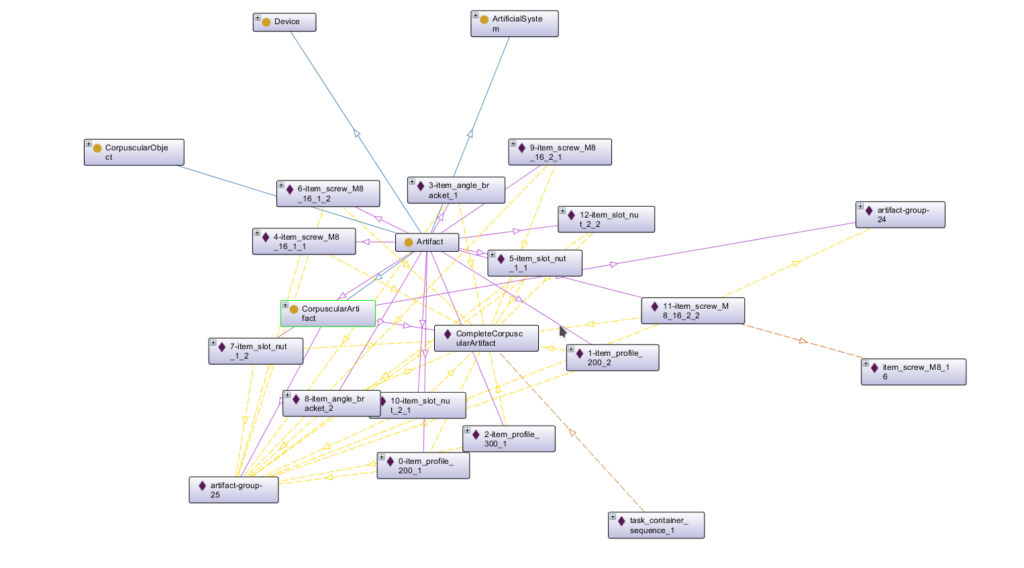
Ansprechpartner:
Philipp M. Schäfer,
Diana Peters
Institut:
Intelligentes Prozessleitsystem
Die Idee dahinter
In der Fabrik der Zukunft werden Produkte in kleinen Losgrößen aus kundenspezifizierten Bauplänen hergestellt. Im Vergleich zu einer Fertigungsstraße, die ein und dasselbe Produkt in Serie produziert, ist hier eine flexible Steuerung nötig, die mit verschiedenen Bauplänen umgehen kann und Aufgaben auf die einzelnen Maschinen dynamisch verteilen kann.
Der Aufbau des Systems
Das am ZLP in Augsburg entwickelte System ist in der Lage, einen Bauplan eines CFK-Bauteils aus einem CAD-System einzulesen und zu verarbeiten. Für jeden einzelnen Zuschnitt gibt es Produktionsschritte, die der Reihe nach abzuarbeiten sind, wie Erstellung des Zuschnitts an einer Cutteranlage, Transport des Zuschnitts in die Produktionszelle, roboterbasiertes Legen des Zuschnitts in eine Form und anschließende Qualitätssicherung. Der gesamte geplante Ablauf sowie der aktuelle Stand werden dem Nutzer visuell dargestellt.
Anwendungen
Das System wurde bereits in der Herstellung von CFK-Demonstratorbauteilen eingesetzt, unter anderem auch beim Bauweisenkolloquium zum zehnjährigen Bestehen des ZLP in Augsburg. Dabei erledigte es alle oben beschriebenen Funktionalitäten bei der Herstellung einer Druckkalotte aus CFK. Darüber hinaus wurde es auch bei internen Forschungsprojekten eingesetzt und wird stetig weiterentwickelt. Hierbei sind zum Beispiel eine weitergehende Ablaufoptimierung und die Behandlung von Fehlerfällen wichtige Themen. Auch das Management von anfallenden Prozessdaten wird in Zukunft eine wichtige Rolle spielen.
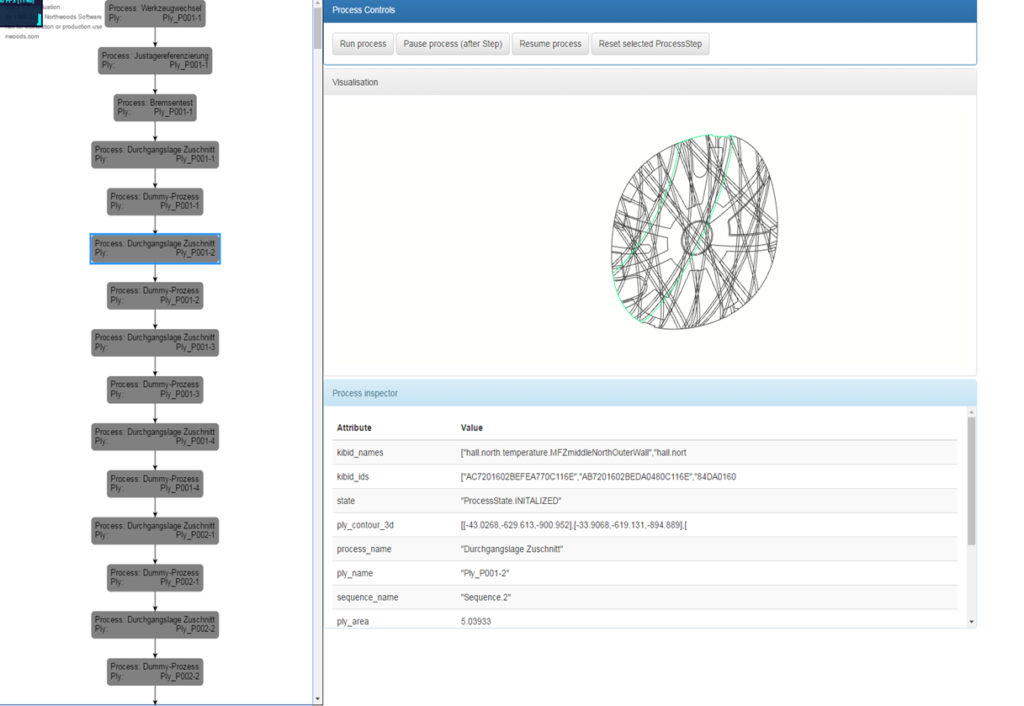
Screenshot des Prozessleitsystems während der Herstellung einer Druckkalotte aus Kohlenstofffaserzuschnitten
Ansprechpartner:
Florian Krebs
Offlineprogrammiersystem für biegeschlaffe Halbzeuge
Die Idee dahinter
Bei der Produktion von Kohlefaserverbundstoffen ist ein wichtiger Schritt die Aufnahme eines zweidimensionalen Zuschnitts aus Kohlefasern und dessen Ablage in einer dreidimensionalen Form.
Der Aufbau des Systems
Das System liest aus einem speziell aufbereiteten Exportfile aus einem CAD-Programm sowohl die 2D- als auch die 3D-Kontur der zu legenden Zuschnitte aus.
Anwendungen
Ursprünglich geplant für das Handling von einfachen kleinen Zuschnitten mit einem Greifer wurde das System weiter entwickelt und kann nun auch mit größeren Zuschnitten umgehen, die von mehreren, auch unterschiedlichen Greifern gegriffen werden müssen. Daneben zeigte es seine Flexibilität, als es auch für die Prozessplanung für das Legen von großen Aluminiumblechen Verwendung fand.
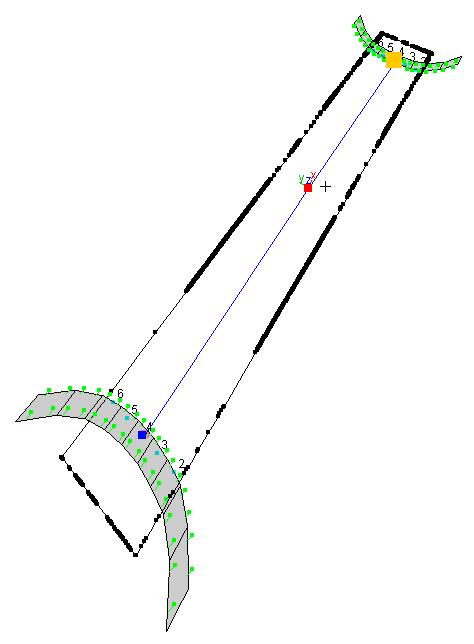
Screenshot des Offlineprogrammiersystems bei der Aufnahem eines Zuschnitts mit zwei gekrümmten Greifern
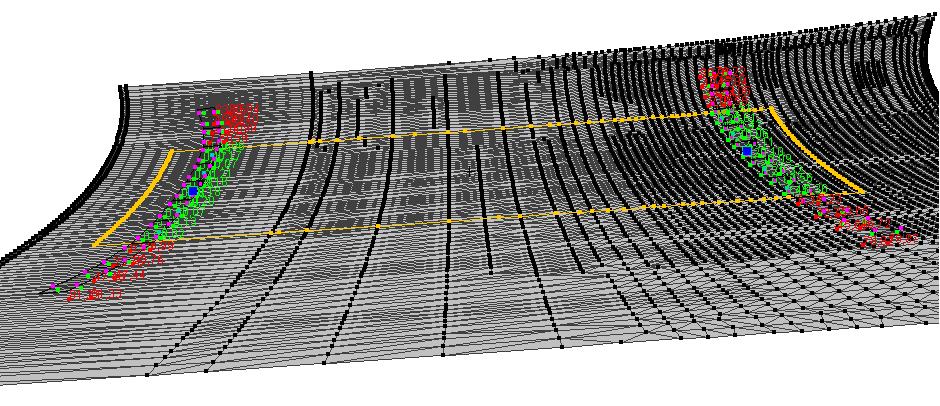
… und der Ablageposition
Ansprechpartner:
Roland Glück
Kollisionsfreie Bahnplanung für kooperierende Roboter
Die Idee dahinter
Bereits jetzt gibt es automatisierte Fertigungsschritte, in denen zwei oder mehr Roboter zusammenarbeiten, um gemeinsam eine Aufgabe zu erledigen.
Der Aufbau des Systems
Das am ZLP in Augsburg entwickelte System kann in einem virtuellen Abbild der Fertigungsumgebung kollisionsfreie Transportpfade finden.
Anwendungen
Das System wird hauptsächlich bei pick-and-place-Anwendungen eingesetzt, bei denen zwei Roboter einen Kohlenstofffaserzuschnitt von einem ebenen Aufnahmetisch in eine dreidimensional gekrümmte Form transportieren müssen. Es ist aber auch in der Lage, kollisionsfreie Bahnen für einen Roboter zu finden und kann daneben für die Handhabung von anderen Materialien wie zum Beispiel Aluminiumblechen verwendet werden.
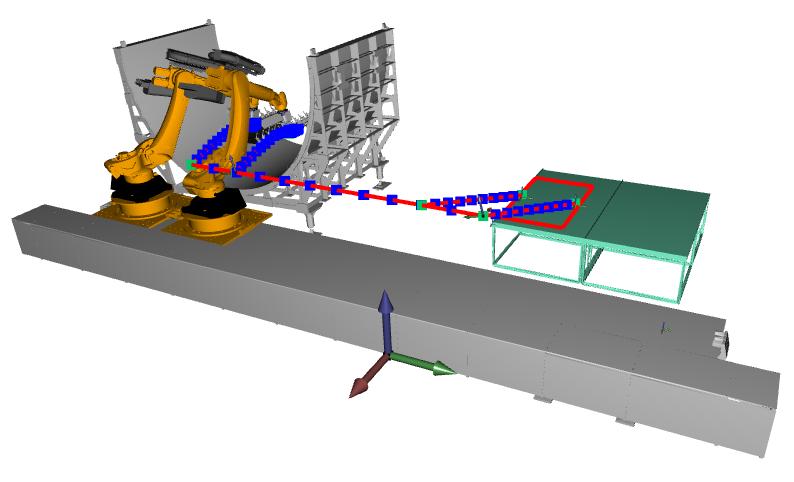
Screenshot des Bahnplanungstools für kooperierende Roboter beim Transport eines Zuschnitts von einem ebenen Tisch in eine zylindrische Halbschale
Ansprechpartner:
Lars Larsen
Der Virtuelle Leitstand
Die Idee dahinter
Produktionsanlagen verfügen traditionell über einen Leitstand mit vielen Monitoren und noch mehr Knöpfen, einem zentralen Leitrechner, in dem alle Informationen zusammenlaufen und einer Software zur Visualisierung der Daten.
Der Aufbau des Systems
Grundlage für den digitalen Zwilling ist ein 3D Modell der Anlage, das als Transportmittel für den digitalen Schatten, also die Visualisierung von Echtzeit-Maschinendaten dient. CAD-Modelle werden oft für Simulationen oder Offline-programmierung verwendet, um bestimmte Funktionen zu testen.
Anwendungen
Mit den Forschungsplattformen am ZLP Stade stehen Multiroboter-Faserlegetechnologien, der größte Forschungsautoklav der Welt und Serienproduktionsline für Strukturbauteile als Pilotanlagen bereit. Sie können sowohl die Rolle eines fiktiven Zulieferers als auch die einer hauseigenen Produktion einnehmen. Lösungen bzgl. End-to-End Kommunikation, Fernüberwachung und Cybersecurity können direkt an vorhandener Hardware getestet werden, ohne den Produktionsbetrieb zu stören.
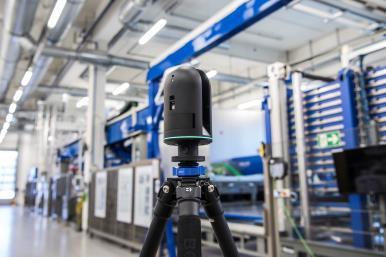
Digitalisierung von Forschungsanlagen: Als Verwaltungsschale für Prozessinformationen wird ein fotorealistisches 3D-Modell der Anlage erzeugt
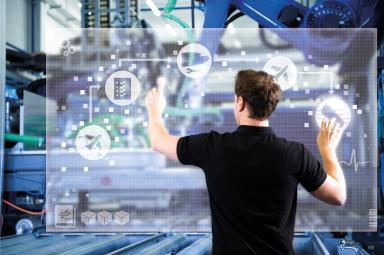
Vision: (Fern-)Bedienung der Forschungsanlage über ihren digitalen Zwilling durch Virtual und Augmented Reality
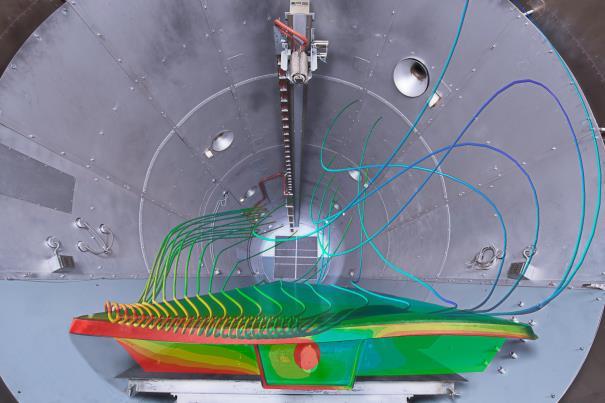
Verknüpfung der realen mit der virtuellen Welt: Strömungslinien und Temperaturprofil am CFK-Flügelwerkzeug im Autoklav
Ansprechpartner:
Dipl.-Ing.(FH) Sven Torstrick-von der Lieth
Institut:
Integrated Positioning System
Die Idee dahinter
In der Industrie 4.0 modernisieren mobile Roboter maßgeblich Produktionsabläufe. Sie gestatten nicht nur einen hohen Autonomiegrad bei höherer Effizienz in routinierten Aufgaben, wie dem Transport von Bauteilen in Lagerhallen und dem Verbauen in Fertigungsstätten, sondern gewährleisten auch die notwendige Flexibilität, um Prozesse umzugestalten.
Der Aufbau des Systems
Das IPS ist speziell für die räumlich-zeitliche Echtzeit-Eigenverortung und 3D-Kartierung in “Indoor”– und “Outdoor”-Umgebungen geschaffen. Im Vordergrund stehen dabei Flexibilität und Autonomie: Für diese Aufgaben werden weder a-priori Wissen über die Umgebung (z.B. Karten), noch externe Referenzierungssysteme (z.B. GNSS) benötigt.
Zur Validierung bestehender Algorithmen und der Entwicklung neuer Ansätze kann das IPS vollständig in der dazugehörigen Simulation synthetisiert werden (Digital Twin). Industrielle Prozesse lassen sich so realitätsnah bewerten und damit verbundene hohe technische, logistische oder ökonomische Aufwendungen vermeiden.
Anwendungen
Die besondere Datenerfassung des IPS‘ erlaubt komplexe optische Analysen industrieller Prozesse. Zum einen können Maschinen auf diese Weise auf Abweichungen vom Normverhalten überwacht, durch Verortung identifiziert und so Unfälle frühzeitig verhindert werden.
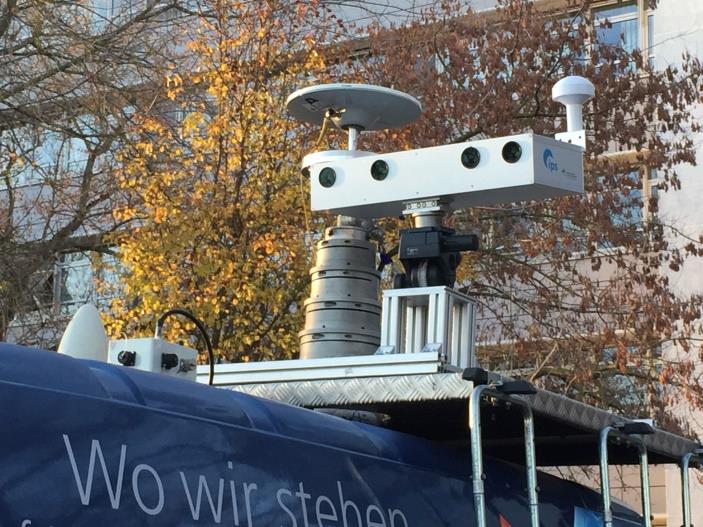
Auf Fahrzeug montiertes IPS
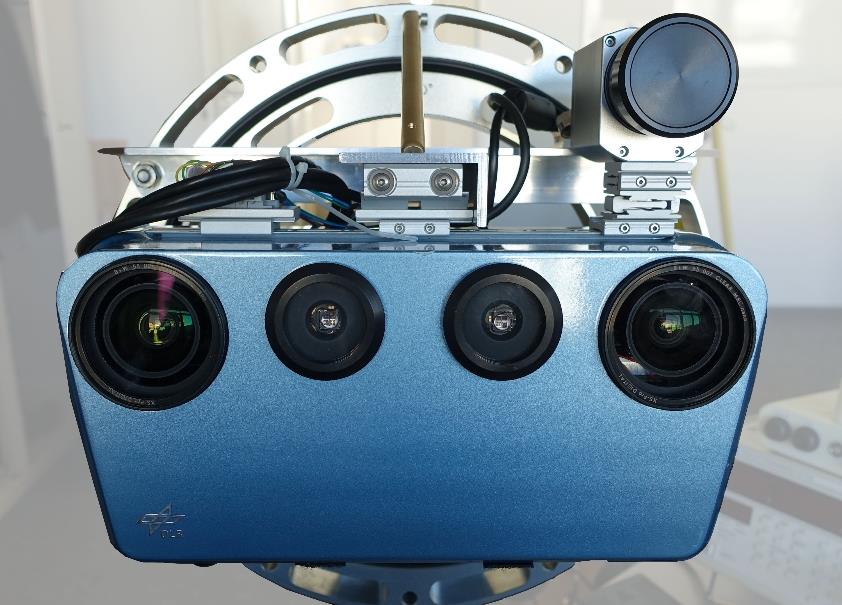
Handgetragenes IPS mit Thermal-Sensor
Ansprechpartner:
Maik Wischow (FoF Ansprechpartner für Technologie)
Dr.-Ing. Anko Börner (Ansprechpartner Institut für Optische Sensorsysteme)